About Our Workshop
Richard Wilson Guitars is the world's largest builder of premium Weissenborn guitars. Richard Wilson personally builds every guitar that comes out of the workshop, from assembly to voicing to lacquering and final setup. He is joined by a small team of luthiers and woodworkers who assist with the preparation of tonewoods and components.
The journey from raw timber through to a stunning guitar is one with hundreds of critical steps. Over the years this process has been refined into what the Richard Wilson Guitars workshop is today: an artform in and of itself.
Every guitar we craft is comprised of hundreds of individual steps that all take place entirely within our boutique workshop in Brisbane, Australia.
Visits to our workshop are by appointment only. Please contact us for more information.
Â
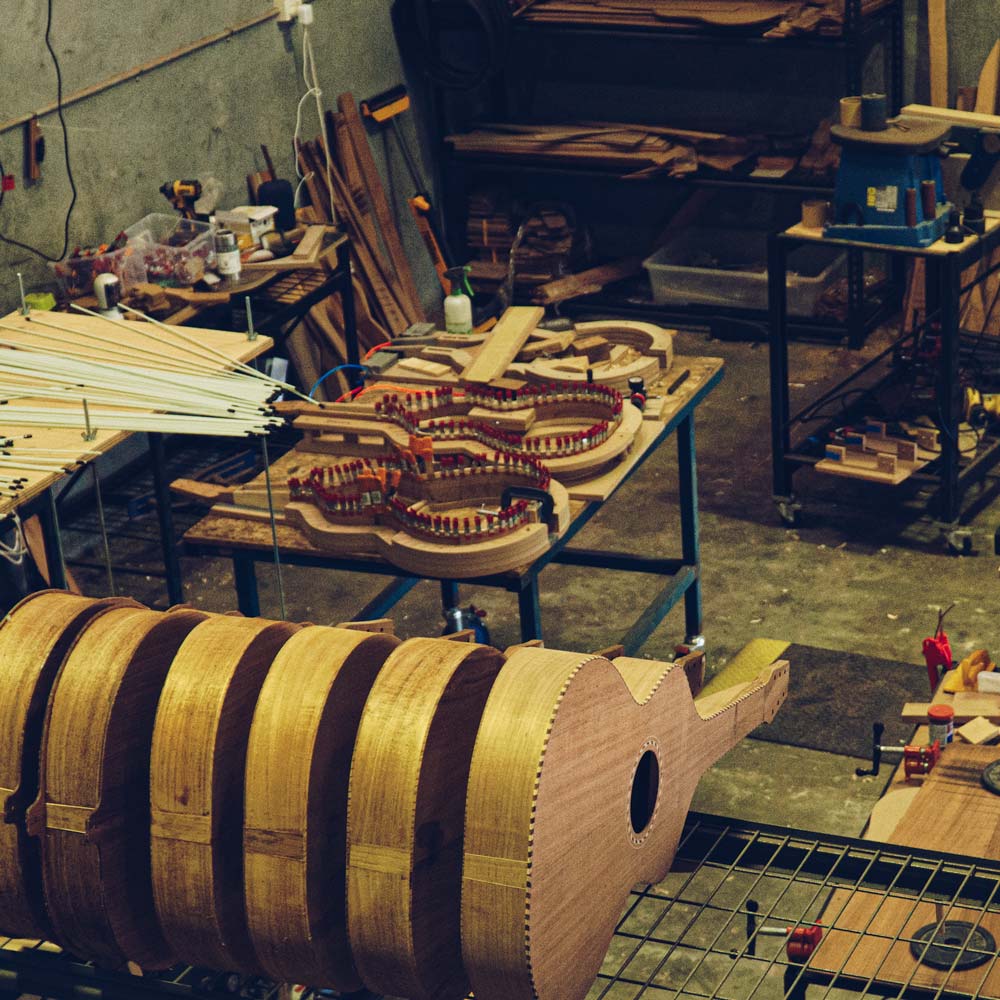
The Space
Instruments are individually handcrafted in a 1600ft² (150m²) dedicated facility. A space that has been designed from the ground up to facilitate the hundreds of steps that go into each instrument.
From traditional woodworking machinery such as bandsaws and sanders through to highly specialised jigs designed by Richard Wilson, every corner of this space is in service of a commitment to crafting the world's finest Weissenborn guitars.
Temperature and humidity control ensures guitars that will stand up to the rigours of global weather fluctuations.
Our workshop is environmentally sustainable with 100% of electricity needs supplied by our 16kW solar PV system.

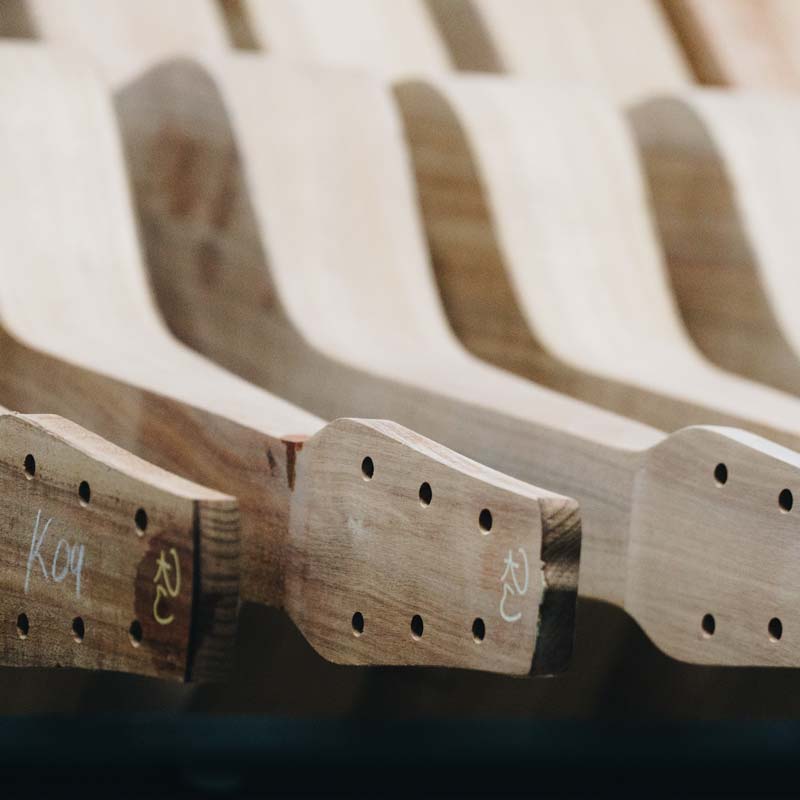
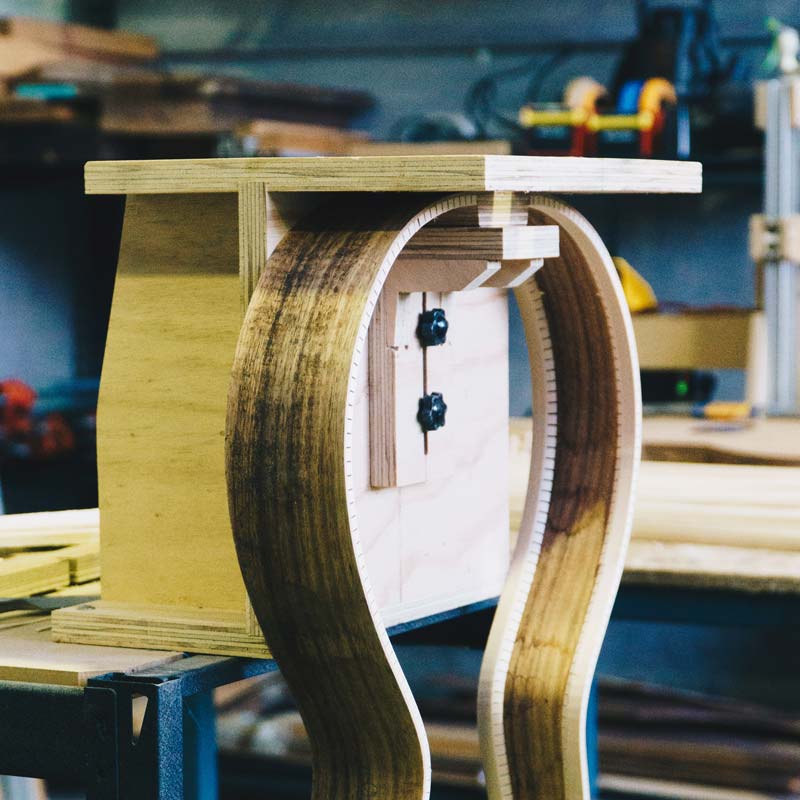
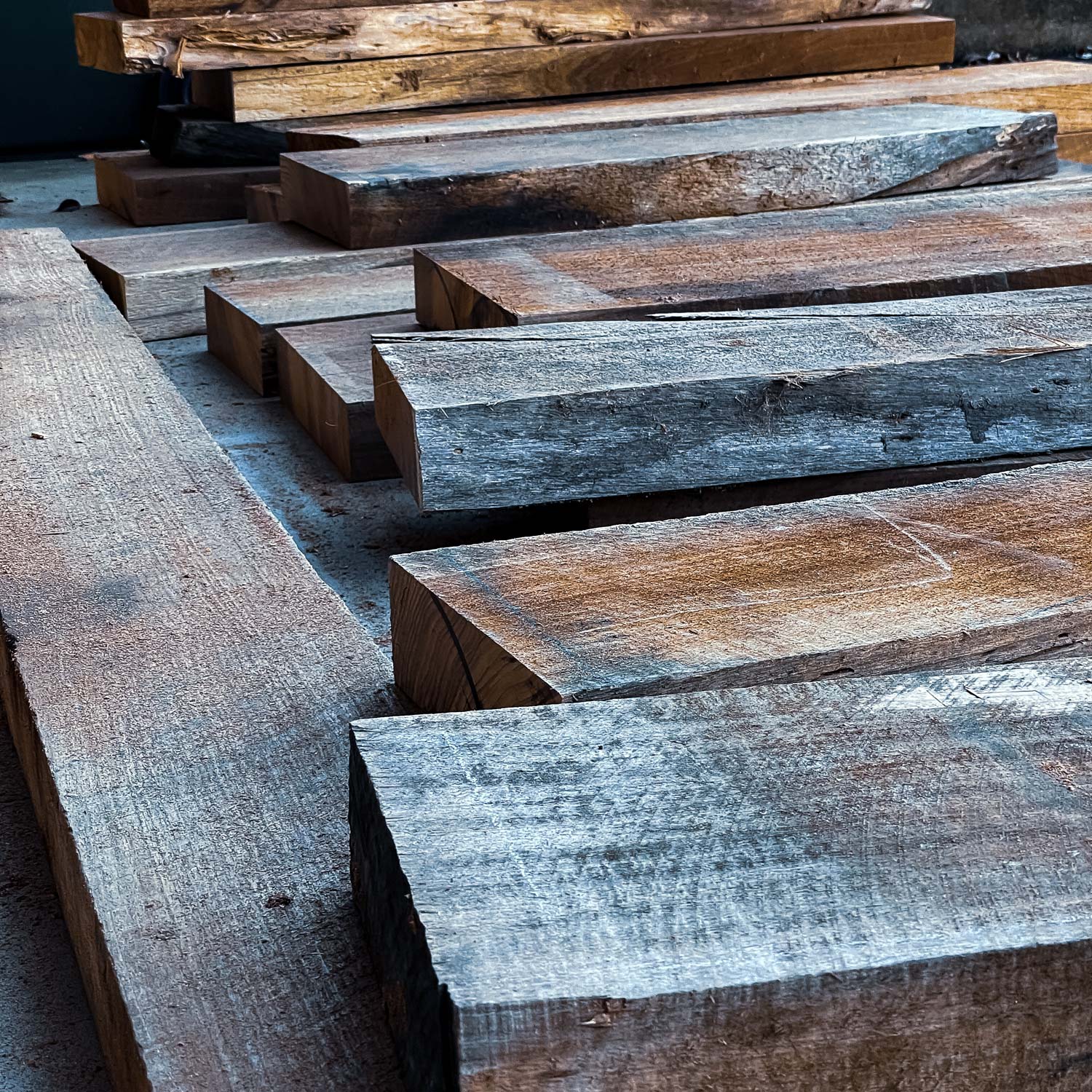
Tonewoods
We source our premium grade tonewoods from both sustainable and salvage sources. We work with passionate suppliers from around the world to find exceptionally beautiful tonewoods, while ensuring this precious natural resource will be available for generations to come.
The tonewoods we source have been air dried, sometimes for in excess of a decade. They undergo a further acclimatisation process inside our workshop. These raw billets of timber will now remain entirely within the workshop environment, leaving only as a completed guitar.
Once the tonewoods reach the optimal moisture content, we resaw down to final book-matched halves on dedicated 20HP horizontal bandsaw.
All woods then undergo another period of air drying before final dimensioning and guitar construction.
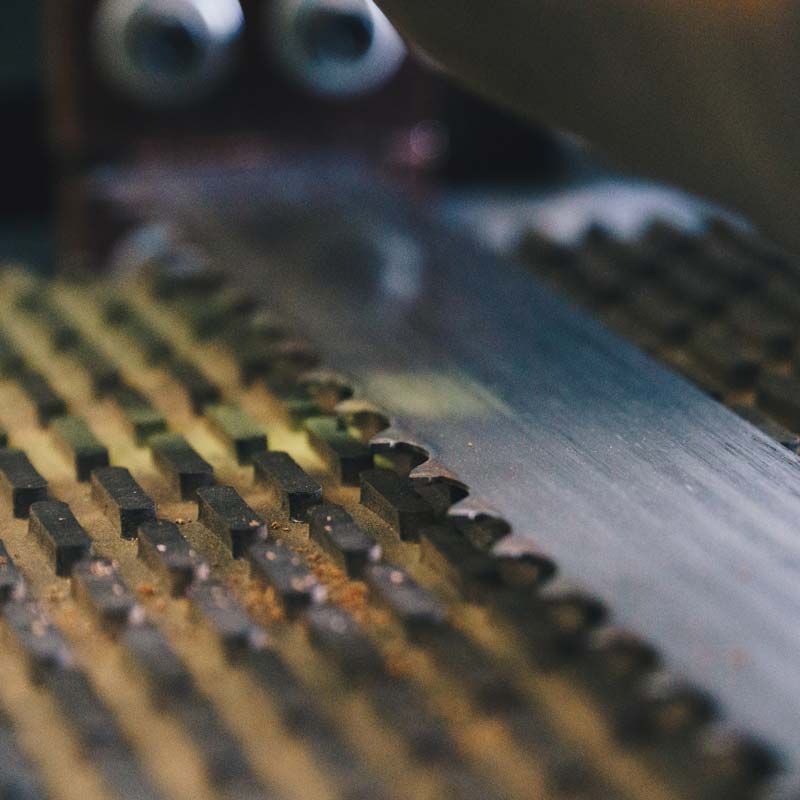
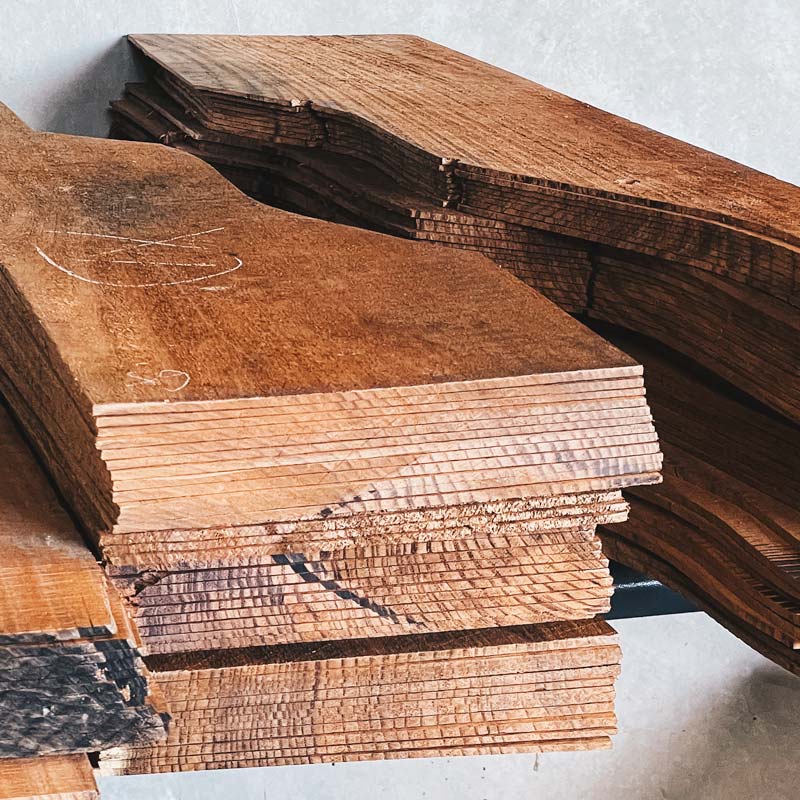
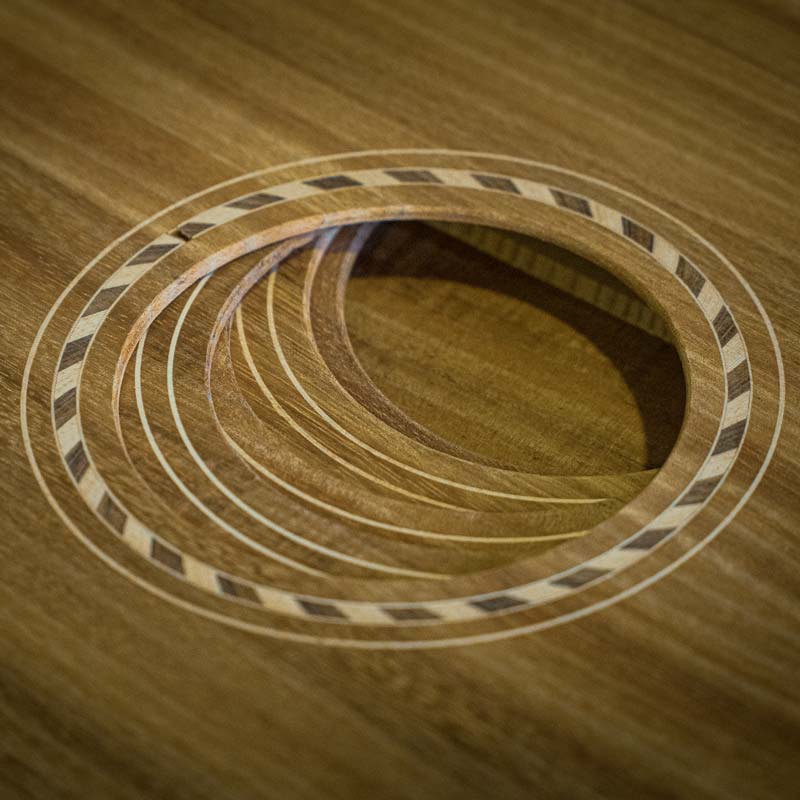
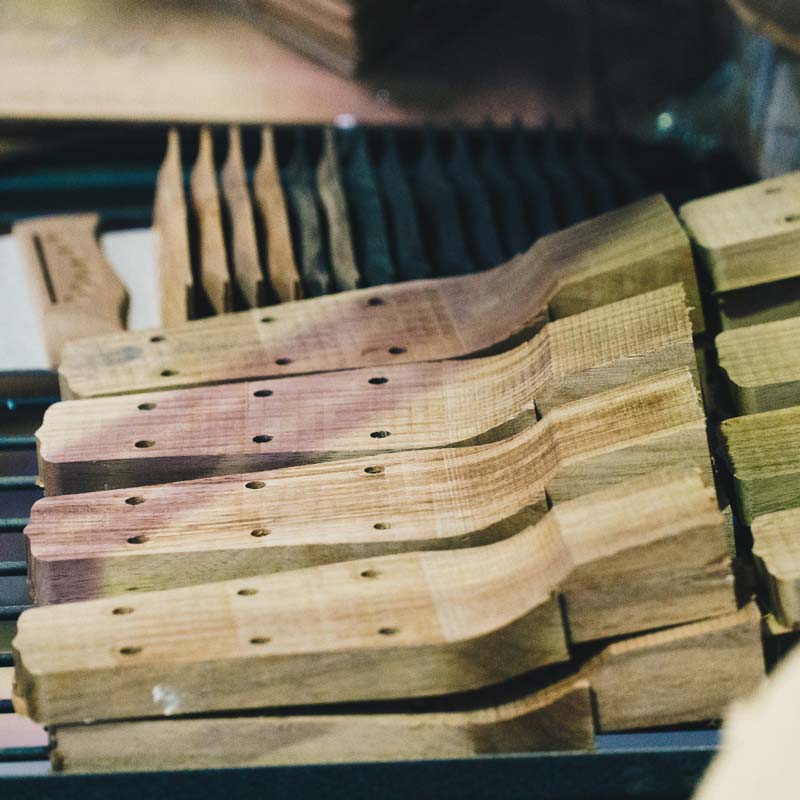
Components
From acclimatised tonewoods, each individual component is meticulously crafted to exacting specifications.
A collection of fixtures and jigs – all designed and built by Richard Wilson – aid in carving headstocks, bridges and fretboards with precision and consistency.
Even the modest and unadorned Style 1 guitar features more than 60 individual components, while the rope binding on the ornate Style 4 contains more than 800 individual segments of wood.


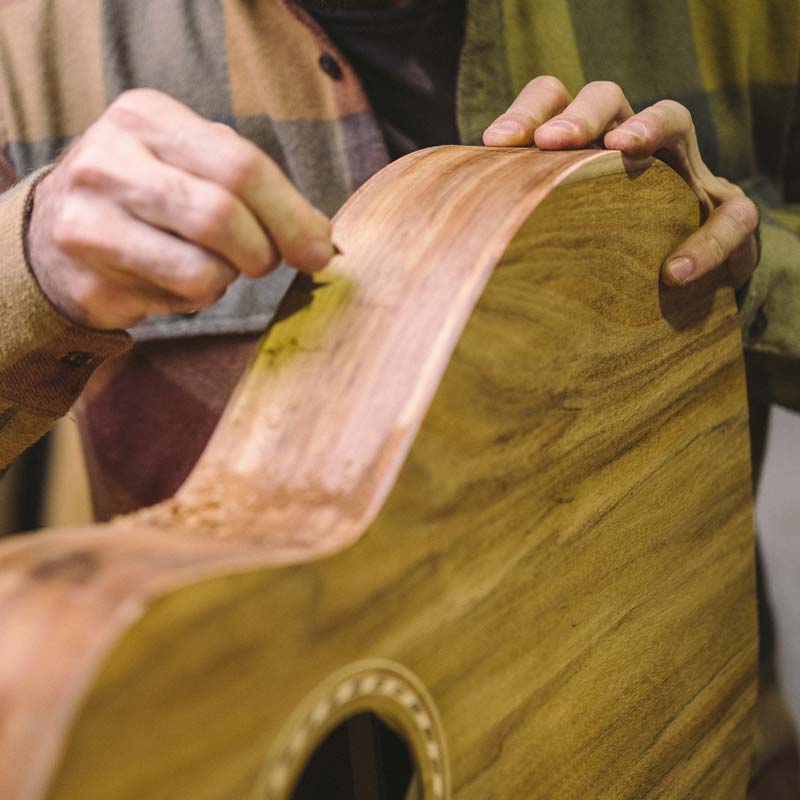
Construction and Setup
Assembly takes place in a humidity and controlled workshop.
Guitar tops and backs are formed from bookmatched halves.
Sides are dimensioned and then painstakingly bent to our iconic Weissenborn shape using a delicate blend of heat and moisture in our unique bending mould. Soundhole rings and rosettes are seamlessly glued into precise channels in the top before being carefully scraped flush.
Soundboards and bracing are individually dimensioned and voiced to ensure each guitar with it a faithful Weissenborn tone yet its own unique character.
Our modern lacquer finish is incredibly thin and flexible. With minimal care it protects the instrument for a lifetime without cracks or checking.
Nuts and saddles are hand shaped and fitted from genuine bone for tone that's warm and full of overtones.
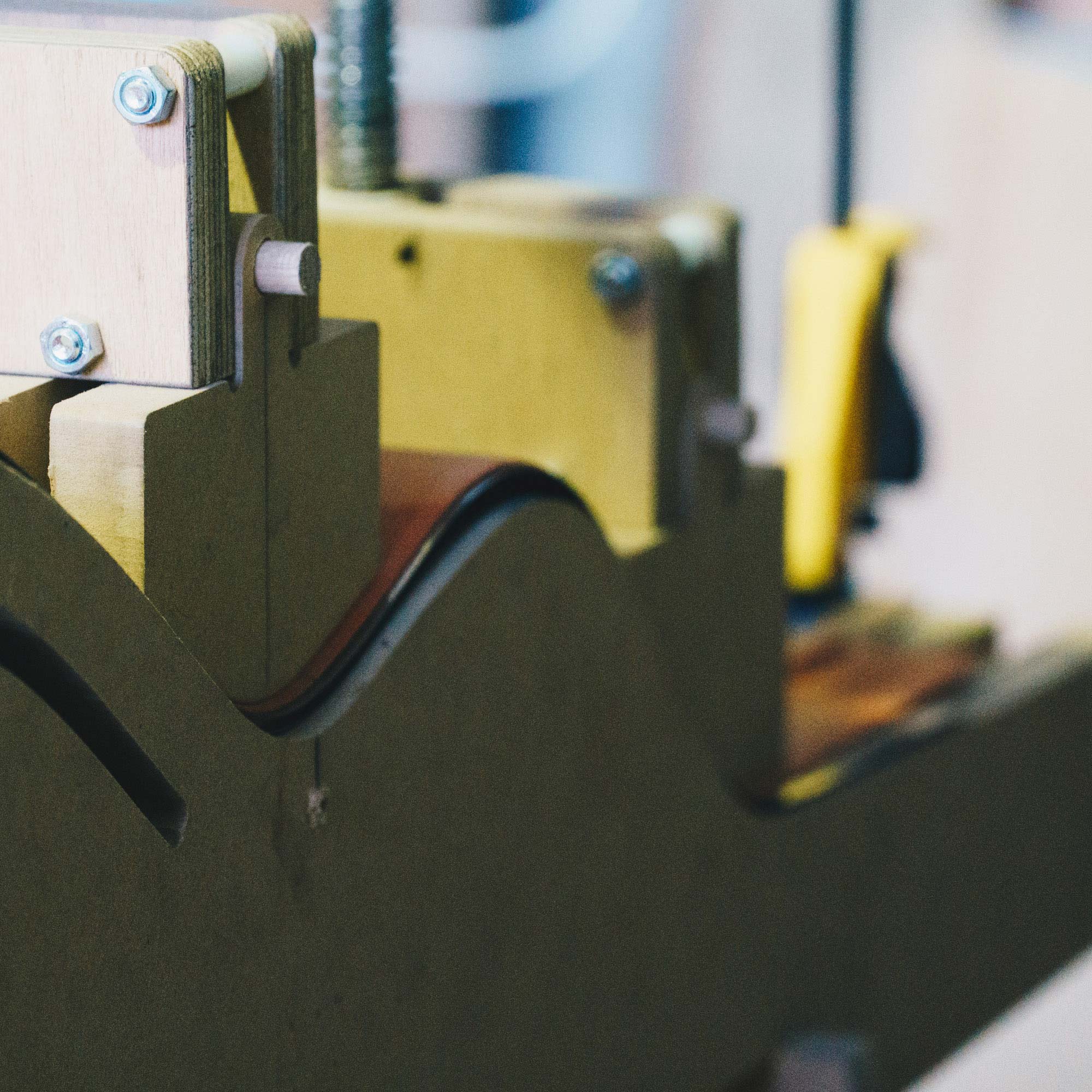
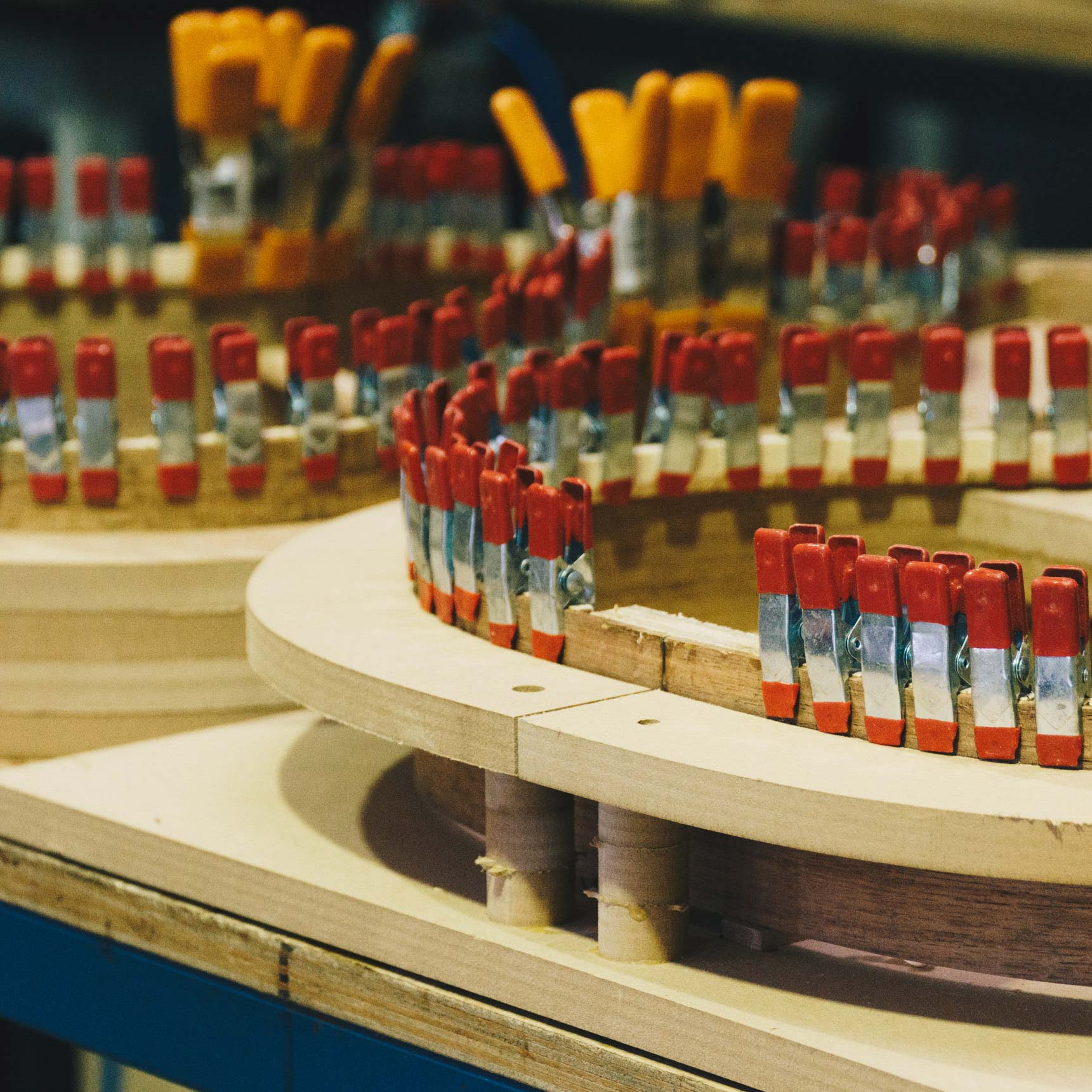
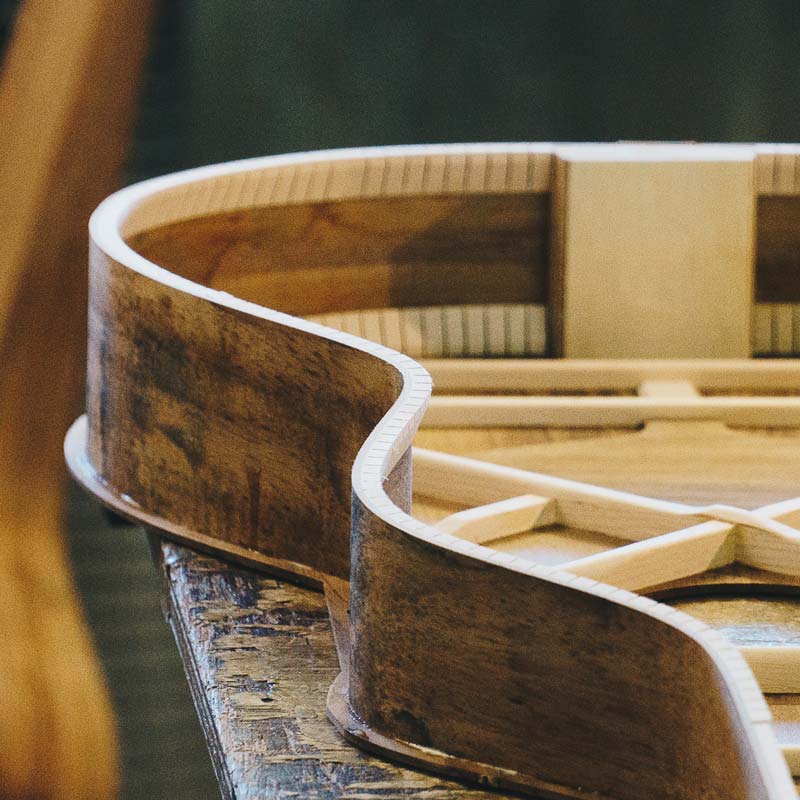